Tube
Shocks
After
reading about my homemade tube shock setup, you'll see I've gone with Doug Jackson's
tube shock setup. Why? You'll also note I'm using his composite
springs, anti-tramp bars and panhard bar. To put all those items together,
I had to use his shock absorber bracket (anti-tramp bars would only work in
conjunction with composite springs if I used it). So, at that point, the only thing left
from my homemade setup was the upper tube shock mount. What the heck, a phone call
to Doug & his upper mounts were on order.
As I'm going with a Hawke's Cars coil-over front suspension that replaces the original shock
with a custom upper control arm, I also decided to match the shocks front and
rear. Thus, I also decided to go with GAZ adjustable coil-over tube shocks
in the rear to match those coming from England. I won't use a coil-over
spring in conjunction with the shock unless I need a small helper spring for the
composites (I'm sure the composite springs will do their job, but I now have a
backup).
And, here's what
I've learned about controlling spring roll-up (or hop) and rear end movement:
Anti-Tramp
& Panhard Bars
Doug Jackson of
British
Automotive sent me a set of his new traction bar brackets to see if
they will work in conjunction with my top hats. His panhard kit is complete and
ready for distribution so it will be one of my major purchases; and, his anti-tramp bars are almost ready for the
market. If his brackets fit, I'll install a set of his new V8 anti-tramp (traction) bars along with tube
shocks.
Here's a couple of photos of one of the brackets attached to the top hats.
It shows the relationship of the spring to the anti-tramp bar.
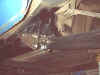
There's still one bolt to put in the rear of the bracket to complete the
installation, I've gotta get a long 21/64" drill bit that'll go completely
through the top hat to do that.
And, the panhard bar and anti-tramps are now
installed.....FINALLY!!!
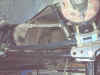
The only difficulty I ran into during the actual installation was adapting the
anti-tramp and composite spring hanger brackets to my top hats. Other than
that, installation of both the anti-tramp bars and the panhard bar were a piece
of cake. Should any of you choose to go the same route, simply follow
Doug's instructions and you'll be finished with the installation of both over a
long weekend.
If things look a bit out of whack in the photos, its because I've not torqued
any of my modifications down; they're in place but waiting toil I can work the
suspension into its normal stance. To do that, I'll put her down on all 4
wheels and roll her around a bit so everything settles into place. Then,
I'll level the panhard bar to a spirit level, and torque everything in place
with the car on its wheels, not jacked up.
While the rear end is out for
its rebuild/modifications {MGC gears in MGB case), I'll also drop the fuel tank
and install a modified one under the center of the trunk area so I'll have room
for dual exhausts.
Fuel Tank Relocation
Ah, the fuel tank. Moving it to
the center of the car from its rightward position creates
enough room to run dual exhausts from the engine to the rear of the car down
both sides of the gas tank while
keeping them high enough not to drag. After all, what’s a V8 car without dual
pipes poking out from under the rear valance?
However, moving the tank
presents a few problems.
To move the tank, new bolt holes
have to be drilled in the trunk floor. That will be easy enough. The hard part
comes when I cut the trunk
floor to move the filler neck opening over to fit the new tank location.
Cutting and relocating the original filler opening in the trunk floor is easy. But, as I want the trunk
floor to look original, I'll have to rebuild some of the raised areas back into
the floor where I make my cuts and patches before prepping for paint.
Since
I also want to maintain the original fuel filling location on the outside of the
car with the tank moved approximately 3", I have to devise a
new fuel delivery setup using a curved gas filler tube and an angled tank filler hose. I will
probably follow Mike Cook's lead and use aviation fuel hose to make the
connection between the original fuel filler location in the body and the new
tank location in the trunk floor.
This is also a good time to send the fuel tank out
to be cleaned and have the fuel sending unit moved. Oh, I'm using a '65-'69
non-vented tank as I don't plan to go the fuel injected route.
Running dual
exhausts on both sides of the car puts a tailpipe too close to the
fuel sending unit. So, my plan is to move the unit to the front of the tank aka
what Nick Smallwood did on his MGBGT V8 conversion with Sebring body
kit and Jaguar XJ6 suspension web site. (Wow! And, I thought I was "the"
autoist! If you want to see some serious MG modifications, visit his
site.)
There's a flat
place on the front center of the tank where the height of the tank is the same
as at the original sending unit location on the side. Placing the unit there and
at the same height from the top of the tank as where it originally was means no
modifications to the sending unit itself. At the same time as we were moving the sending
unit, I had the tank boiled and relined. Here's what that modified tank looks
like.

So
here's the procedure for centering the gas tank under the trunk floor:
1. Make a brown paper template of the
top of the gas tank, marking each hole location. Don't forget to mark the
inlet tube location: make that hole the same size as the large one in the trunk
floor through which the tube protrudes.
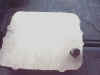
2. Place the gas tank template over the
trunk floor so that the holes in it and the factory gas tank bolt holes in the trunk
floor line up.
3. Move the template 3-1/4" to the
left and mark the new bolt hole locations and the new inlet tube location.
4. Start with a 1/8" drill bit and
make 10 guide holes--4 on each side & 2 along the back of the car.
5. Move upwards in bit sizes re-drilling
the holes until the last size is 1/2". Don't forget to sand off any
metal residue from your drilling.
6. Under the car, cut off the 2 studs on
each side that protrude through the trunk floor to hold the gas tank. With
an orbital sander, grind them flush with the trunk floor.
7. Cut the rear exhaust hanger bracket
off flush with the rear valance as :
a. its in the wrong place
after the tank is moved, and
b. it interferes with the
movement of the tank.
8. Cut a large rectangle out of the
trunk floor from the right edge of the flat part of the floor to about 1"
left of where you marked for the new location of the fuel tank inlet tube.
9. From underneath the trunk floor,
align the gas tank with the new holes.
10. From inside the trunk, and using
5/16"x1" fine thread bolts with a flat washer large enough to cover
the 1/2" hole, run the bolts through the gas tank holes that have threaded
hardware attached to them (2 on each side & the 2 in the rear).
Finally, put 4 bolts through the holes that earlier were where studs went &
attach them from underneath using flat washers, lock washers, and nuts.
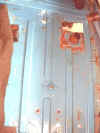
11. Spot weld the 4 gas tank side bolts that were
attached using nuts in #10 above--not those attached using hardware integral to
the tank--so that they replicate the studs that were permanently protruding
through the trunk floor.
12. Finally, weld the large square of
trunk floor around the gas inlet tube and, using welding washers, fill all
original holes.
PHOTO
13. And, the last thing is to form a
piece of aircraft hose to go between the gas tank inlet tube and the filler neck
ferrule.
PHOTO
14. Then, remove everything, clean and
undercoat the trunk floor above the gas tank, and reinstall the gas tank making
sure you use some type of body sealer under all the flat washers.
15. Last, sand the trunk floor to remove
any evidence of welding; and, using body putty, reform the ends of the raised
ribs cut and replaced during the project.
PHOTO
Now, all that's left is to paint the trunk
floor. Oh, if you're gonna use a vented gas tank system, you'll have to
cut the hole for the vapor separator to gas tank hose.
Me?
Not
emissions control #1 will be in this baby!
I'm going with an early vented
gas cap.
I
said, "all that's left is to paint the trunk
floor." That's not quite true. All that's left of the fuel
tank relocation project after each step listed above is completed is to paint
the trunk floor. But, the fuel lines, brake lines, and wiring harness have to be
moved out of the way of the right exhaust pipe. More to come on that
project as I get into it.
Wiring will be easy; I'll just reroute it and run it inside the car like Rover
did with the RV8 (along the center console under the carpet). Go to the section on
wiring
modifications to follow that project as it develops.
While I'm waiting on rear end parts to arrive, I'll weld the "top hats" I had
built by a local machine shop to the undercarriage of my '79.
"Top hats" provide additional chassis
strengthening aka those installed by Rover on the RV8 body shell. Adrian Salisbury of Leicester,
England faxed me a set of
the original build plans.
The "top hats" provide extra strength for the front spring hanger
spread from the frame cross member in front of the seats to the spring hanger
itself. Plus, the "top hats" provide extra support for the anti-tramp bars I plan to install. So, I took the mockup and
Adrian's drawings to my local machine shop for fabrication.

An initial test fitting shows they will
fit perfectly after I grind off a convex 'dimple' on either side of
the front spring hanger location, shape the front edges to fit where body panels
were welded together at the factory, and drill a hole through the "top
hats" for the spring bolt. Additionally, the original frame cross member
must be drilled to accept a bolt at the front of the top hat. The car will then be ready to
accept new springs and the modified MGB rear end.
Well, here they are: the top hats are test fitted. Man, they look great!

(Left Top Hat Before Welding)
Finally, they're welded underneath.
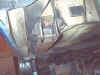
And, here they are undercoated with
spring/anti-tramp bar bracket attached.
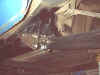
But,
before we move any farther with my car, here's an article on how to make a tube shock
conversion at home if you're so inclined:
|
Converting the rear
suspension to tube
shocks is so easy it’s scary, and there’s no need to purchase an
expensive kit. Just click on Skye Poier's web site: The
MG Experience.
On his "service page" are some great tech
tips, including how to convert the rear to tube shocks. A
couple of them, the one by Dave Tietz and its modification by Rick Morrison, are
the ones I used--along with a small modification of my own.
The conversion can be made with a few new bolts and
3 simple
pieces of 3/16 steel plate at each upper shock mount.

Here's my parts list:
1. 2 - 21/4"x1/2" Grade 8 bolts
2. 2 - 1/2" Grade 8 lock
nuts
3. 4 - 1/2" flat washers
4. 4 - 51/2"x7/16"
Grade 8 bolts
5. 4 - 7/16" lock nuts
6. 4 - 7/16" fender
washers
7. 12 - 7/16" flat washers
8. 2 - 7/16" ID steel
tubes cut to same length as upper
shock mount tube
9. 2 - OE lower shock absorber
brackets
10. 6 - pieces of 3/8" metal cut to
shape of OE shock
drilled w/7/16" holes
11. 2 - Gabriel Red Ryder Gas
Slim Line shocks
(# 81108) found at CarQuest (# SHK-47334)
Total cost including shocks: $75 & change (8% sales tax) & that
includes $20 to machine shop for cutting/drilling metal plates.
As I read and reread everything I could about rear shock conversions, I became
more convinced that Gabriel shocks are best for this setup, more for ride comfort
than anything. Visiting local Gabriel dealers, I learned that CarQuest
carries the exact same shock that's been repackaged under their brand name--and, at a
lower price! Sure enough, the boxes in which my shocks came read "by
Gabriel" and the shocks carry Gabriel markings.
Okay, now for installation:
The original lower shock absorber
arm bracket is flipped over and switched side-to-side on the car so that the
bend is down instead of up with the shock absorber mounting hole still on the
inside of the spring.
One modification I made to
that setup was to bend the shock mounting point so that
it comes out at an even 90-degrees from the flat part of the bracket (when
flipped over, it splays out so the shock doesn't mount exactly straight), and I
chamfered the center locating hole for the spring. The 21/4" bolts,
flat washers, and lock nuts are used to hold the bottom of the shock to the
shock absorber arm bracket.
The 3/8" pieces of metal are used on
either side of the frame and on the outside of the shock (I used 3M sealing
compound between the frame and pieces of metal). Fender washers are used
on the outside of the piece of metal with bolts inserted through them from the
outside of the frame.
 On the inside of the frame, 7/16" flat washers are placed against the flat
piece of metal. The steel tube is placed over the rearmost bolt and the
shock over the front bolt with 7/16" flat washers against the shock and
tube before the third piece of 3/8" metal is bolted down using lock nuts.
Voila! Modern tube shocks!
And, if one ever wanted to, the car could be converted back to original
equipment shocks.
|
|