If your car needs new floors and you
don't have access to a welder, or more importantly, you don't feel your
welding skills are up to the job, there is a new generation of body glue
products that claim the resulting joint is actually stronger than the
surrounding steel. The product I used for my car is called FUSOR,
but there are products by 3M and DURAMAX that are basically the same thing
and should be equally effective.
Rust usually starts from the top down in
roadsters. My floors looked like this:
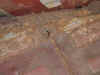
Another view:
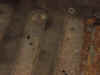
To use any of the glue products, you
basically need to have enough good metal to leave a 1" flange around
the outside, so that you have a place to run a bead of glue. If your sills
aren't in good shape this is not a good solution. If they are, read on.
Since my floors weren't as bad as some, I
elected to remove only the high ribs and leave all of the lower metal
which was in really good shape
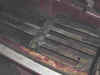
To do this, I used an cutter wheel on an
air powered cutter, although you could use other tools, such as a cutoff
wheel on a grinder, or even a metal blade on a jigsaw. Before undertaking
this step take a look under your car and notice the location of the cross
members, brake lines and other things that run under the floors. I
didn't and now I need new brake lines. Also make sure you wear proper safety
equipment, safety glasses and gloves are the minimum.
Cleaning the old flanges to bare metal is
the next step. I used a wire wheel on a grinder to remove most of the rust
followed by some 40 grit on my DA to get it all shiny. My DPO had done
this job previously on the left side, and used a ton of seam sealer.
Unfortunately,
the only way to get rid of it is elbow grease. I found that a heat gun
softened it up enough to scrape, followed again by the wire brush.
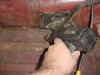
Turning my attention to the new
floorboards, because of the way I trimmed my car, I had to do a bit of
cutting on them also. Anything that interfered with the old floor pans was
removed,
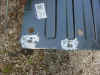
And all the factory primer was cleaned
off to give a clean metal surface for the glue to bond to.
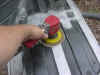 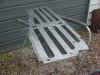
Notice that I used British Heritage floor pans. They come with the captive nuts for the seat rails already
installed. Others, such as Steelcraft are cheaper, but you have to install
the nuts yourself.
After test fitting your panels several
times to make absolutely certain they fit, apply a 3/8 bead of glue
to the flanges using the applicator gun. Yes, you have to buy a special one
and it costs about $50, still cheap if you don't weld. Since enough is
good, more should be better, and I applied plenty. Probably wasteful, but
these floors aren't going anywhere.
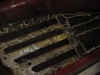
Place the new metal in place and use a
few self tapping sheet metal screws to hold it in place while the glue dries,
and you are done. Time to admire your craftsmanship and have a cold one.
When the glue is dry apply some brushable seam sealer and reassemble your
interior
It took me about two weekends to complete
what I anticipated to take about two days. What doesn't. I feel the floors
will be there forever, so I painted the top and bottom with POR15. The
glue fills the seams from within and should keep rust causing moisture and
dirt out.
theAutoist's NOTE:
The thing I did differently from Chuck is I removed my entire old floor
pans, leaving about 1" of the old floors as a lip to attach the new
floors. That 1" lip was where I applied my Fusor - both around
the edges and along the center floor cross members.
Also, Chuck used sheet metal screws to hold/compress the floors in place
until the Fusor dried. I prefer rivets that can be left in place
permanently.
The table below illustrates uses of and drying time for Fusor 110B/11B,
the medium drying product. There is also a fast drying and slow
drying Fusor.
|
110B/11B
Fusor Metal Patch Panel Adhesive Bondline Control
(Fast-Set)
|
Substrates
Installation and bonding of unprimed metals
including aluminum
Applications
Patch panel bonding and bonding of dissimilar
metals, cab corners, panel sections and aluminum
trailer repair patches
|
• Designed to create
uniform bondline thickness despite differences in
clamping techniques
• Quickly bonds metal patch panels without welding
or pop rivets
• Built-in color indicator; turns from beige to
green as adhesive cures
• Tough, modified acrylic formula with the same
proven performance characteristics as our OEM door
skin hemflange adhesive used on more than 10 million
cars and trucks
OEM Approvals
GM: Panel replacement per TSB#02-08-98-001A, meets
GM6449G
DCX: Weld bonding per #81-170-03005
Nissan: NTB96-034A
Available Sizes: 7.6 oz
(225 ml) / 1.7 oz (50 ml)
|
|
|
|
|
|