The guys at the body shop have gotten together and developed their plan
of attack. They're starting on the rear of the car and will work
forward. First thing they're doing is smoothing the rear quarters
(eliminating the side trim line and smoothing the tops of the rear
quarters by eliminating the fender bead) and reshaping the rear wheel
arches into rounded arches; they're also taking molds off a late-model
7-series BMW's front wheel arch flares - those are the flares they'll
use all around my car, just 1/4" wider on front than on
rear.
And as they work the fiberglass Sebring rear valance onto my car,
they're also smoothing the rear end of the car and removing the stock
MGB gas filler location. They're also cutting holes in the Sebring
valance so my dual exhaust will exit through the valance rather than
under it (ala the '65 Mustang GT - actually, they're using '65 GT trim
rings to finish off the holes they're cutting.).
Since the overall plan calls for shaving the door handles and trunk lid
push, they're also doing some fiberglass work on the trunk lid.
It'll end up with a built in air dam (ala the new Miata) that
incorporates a third brake light.
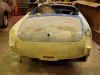
|
The custom rear
Sebring valance is in place. Notice the recessed license
plate. There's still lots to be done here: the exhaust ports have to be cut through the valance on either
side of the license plate; and the 3rd brake light and
integrated spoiler have to be molded onto the trunk lid along
with license plate lights in the recessed area. Did you
notice there's no gas filler opening hanging onto her butt like
a hemorrhoid? More on that mod a few photos below.
|
Taillights? Early 2-piece European
amber upper/red lower MGB units - like she was originally
designed to have! Additionally,
the rear wheel arches still have to be rounded and the 1"
fiberglass flares installed. There's lots left to do back
here. This is only step 1.
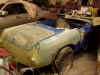
|
And the top edges of
the fenders have been smoothed. To accomplish that, we
removed the fender beading, welded the seam, and laid a thin coat
of fiberglass before smoothing with body filler. All so
she'll never crack. Even without paint, its clear to see
this will be one of the mods that stands out. Shades of tiny fins! |
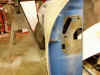
|
Look, Ma! No
door handle! That's right! We're going to use electric
solenoids so the doors and trunk open by remote control. No going back
to original from these mods! Look at the edge of the door to
see how cleanly the body guys smoothed the trim line ridge - lots of
slicing, smoothing, and welding to that job! |
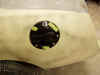
|
Okay, this is what
you really want to see: the 2003 Hyundai Tiburon gas filler welded
and blended onto the MGB's rear quarter (yep, driver's side; we're
also modifying the gas tank to match the new location.)
Looks
like it was designed to be there, eh?
Just wait till you see
the photos of the inside of the trunk area where the filler is
tied into the MG's gas tank, and how its neck is hidden by the MGB
GT hatch floor that's also being grafted onto the car. That
new trunk floor will be covered in detail once we get to
it.
CAUTION:
This mod
is not for the weak! Do not attempt it at home.
There's much more behind the panel than what you see here:
attaching the neck itself, modifying the gas tank, fitting the
overflow pipe through the body, etc.. All work was done by
professionals using proper safety equipment.
|
The front of the car? You'll just have to hold your breath! I
will, however, give you a little peek at some of the changes to the
front. Here's my custom fiberglass MGC hood after we've started
modifying
it. And we're still not through.
After looking at it at this point, the consensus in the shop was to smooth out the
chrome line at the front of the MGC hump so it and the chrome strip are
eliminated and the hood becomes 'shaved'. That'll happen this week. 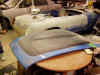
Oh, if you're wondering - fiberglass GT6 scoop
on top of MGC hood
In the background of the photos you can see my car with one of the
taillights installed. Right now, they're cleaning up around them so
there'll only be about a 1/8" gap where they meet the body. 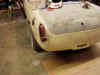
I also went by the Harley Davidson dealer to discuss rearview
mirrors. I want something small that harkens back to the early
fender-mounted mirrors of the '50's and '60's but that are small enough to not stand out when
mounted on the
doors. The parts guy showed me several sets of mirrors and I found
one I really like, except it says "Harley Davidson" on the
stem. So, into the parts room he went and came out with a set of
aftermarket, short stem mirrors that will look great on the car - no H-D
logo either! They'll be test mounted soon.
Finally, I gave my go ahead for the rear wheel well flares. We're
going with a 1" flare back there. I'm going to remove the gas tank and take it to
the radiator shop for
modifications so it fits the Tiburon gas filler on the driver quarter. I'm also
taking an MGB GT hatch floor to the body shop so they can start building/welding in
the GT floor supports into the roadster's trunk and then get it fitted. Radical.
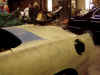
Plus, the hood is also changing. The
easiest way to show that transformation is with photos.
From
this: |
|
To
this: |
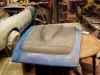 |
To
this: |
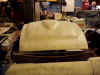 |
If you're wondering: in the left photo above is the custom MGC
fiberglass hood I had British American make. It has the entire
center section raised a couple of inches. In the center photo is the
same hood with a custom fiberglass GT6 scoop added. And in the right
photo is the same hood with the front MGC chrome section smoothed.
Here are a few more photos that show the hood's details. The first
one shows the openings in the rear that will act as a type of cowl
induction, pulling hot air from the rear of the engine compartment. We've
manufactured small grilles to go inside them Those grilles mimic
what will be installed inside the original MGB grille.
Rounding rear
wheel arches/making their flares:
Remember, we pulled molds off the rear wheel well flares
of a late-model 7-series BMW. That gave us the outside design of the
flares we'll use on my car - 1" in the rear; 1-1/2" in the
front. But, it doesn't give us the overall 3-dimensional shape of
the flares.
First, however, before flares can be molded to the car, we have to cut my
wheel wells to match the basic shape of the flares. To do that,
we're rounding the arches. The photos below show you the
protractor my master body man made to get the rounded wheel arch shape. From the center of the rear hub, they moved upwards 2"
and made a cardboard ruler that split the original wheel arch at both bottom
corners. Drawing along the arch from those bottom points, the
protractor raised the center of the wheel arch 3" as it rounded it.
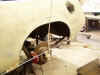
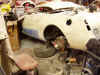
|
Next the outer
quarter panel was cut to the line drawn with the protractor and a
new lip formed and turned under.
Then, the inner fender was hammered up to meet the new edge of the
quarter panel and the two welded together. VOILA!
Round wheel arches! And once the undercoating is applied to
the fender well, you'll never see the hammer marks. |
Here's
what the new wheel arch looks like with a 14" x 6-1/2" wheel installed (though the car
is still jacked up, the effect is clearly evident). And remember,
we're going to an even larger wheel once the car is on the road. 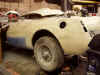
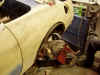
|
To make the under lip
(bottom side) of the wheel arch flare, we first made a metal arch
pattern that will be welded to the fender itself. Then it
will be sealed to the body (top and bottom( with epoxy to keep
moisture out. |
And
here's what the flare contour will look like from the rear of the
car: 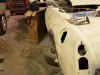
15
Mar 04: Since
the last time I was at the body shop, foam has been glued to the rear
quarter and then shaped to match the contours of the wheel well flare
we pulled from the BMW. Then, a layer of fiberglass cloth
was laid up over the foam and smoothed to blend into the body while
maintaining the basic shape of the BMW flares.
In its final phase of smoothing, here's what the rear flare looks
like. After smoothing is finished, the rear quarter will be primed
and work will begin on the opposite flare.
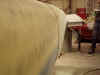
So, there's the basic read wheel well arch after its rounded and
flared. Subtle yet it draws your eyes right to the flare.
Well, both
rear flares are finished and the third brake light housing is shaping up;
so, work inside the trunk can begin. We've got to reshape the trunk
floor for the relocated gas filler....
However, what you really want to see is the
front end; so, here's a photo and then I'll walk through the process for
the conversion. 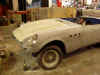
Yep! New Mini headlight buckets,
smoothed side body line, fender flares, and '49 Buick port holes to vent
heat from the engine compartment. And I'm here to tell you: unless I
see the car in person, I don't believe another exists anywhere in the
world with this headlight modification! Especially not utilizing steel fenders. Lemme show you
why I say that:
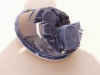 |
Here's the backside
of a Mini headlight bucket. How do you attach it to an MGB
fender? |
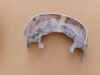 |
Well, you fabricate a
fiberglass bracket! |
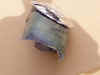 |
|
However, then you have to cut and shape the fender. And I
don't mean just whacking a chunk out so the headlight fits.
The entire front shape of the fender has to change as does the 'valley'
along the top of the fender at the hood line. Also, do you see the difference between the cut driver
side fender and the uncut passenger side fender? Look at the
amount of fender showing between the headlight and edge of the
grille opening. |
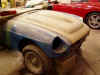 |
Again, in these
photos you can see the difference as the area in front of the
headlight is being rebuilt. The cut driver side fender has a
much wider 'scoop' in front of the headlight and ends up much
closer to the grille opening.. |
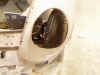 |
Here's the final
roughed in opening. It is designed so the headlight bucket
fits flush. And, if you look closely, you can see where the
outer edge of the fender has also been widened to accept the
bucket. Its almost not noticeable because of how the widened
portion flows into the fender flare. |
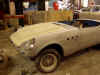 |
Again, the final
'roughed in' look. Kinky enough to be sexy. With my
custom hood, the lines of the headlight flow pretty neatly - in my
opinion - and my opinion is the only one that matters!. This
car just looks MEAN! |
|
And here's a photo of
the front fender flare and the '49 Buick port holes. You
know, there'll not be an MG logo anywhere on the body of the car
when its finished. Wonder what the uninitiated will think it
is? |
How
long did it take. This 1 fender took 2-man weeks of labor! The
second one took about 3 days. So, this is definitely a modification
to be carried out by the professional body man. And my body men have
decided they wouldn't want to do this in metal!

|