When
you are checking wheel bearings you don't have to take the bearings completely
out unless you see something wrong.cup".
When
you remove the spindle nut and pull the hub the outer cone will fall out.
To remove the inner cone you must remove the seal. Wipe the area clean with an
old rag and remove the seal by prying it with a large screwdriver. Note the
orientation of the seal lip in relation to the hub and always replace the
removed seal with a new one.
Clean and inspect all cones that mate to a good cup by wiping away excess
grease with an old rag and washing them in solvent. A convenient and safe
solvent for this, and several other jobs, is plain old cheap paint thinner;
often called naphtha or mineral spirits. Wash the cones in the solvent with a
small brush like a paint brush or parts cleaning brush and by swishing them
and rotating the caged rollers while submerged. When good and clean they can
be dried with compressed air, a hair dryer, or by simply letting them air dry.
When dry, closely inspect all the rollers for any sign of pitting or
foreign matter pressed into the surface.
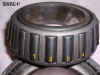 |
This bearing is near the limits of
wear, but is acceptable for many thousands of miles of dependable
service with proper lubrication. Rollers #1 and #4 and the one just
past #4 are typical wear patterns you are likely to find on any
roller bearing that has seen some service. Rollers #2 and #3 are approaching
the limits of what I'll re-use but OK because there is nothing there
that can collect debris or pinch through the lubricant recommended
with this bearing. Every roller has been turned and closely
inspected, #2 and #3 are the worst ones on the bearing. The
discoloration inside the bearing doesn't amount to anything. That
area is not a working part of the bearing and just slips onto the
spindle.
|
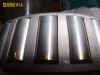 |
This is a close-up of bearing #1
so you can see the condition of rollers #2 and #3 as they really
are. Lighting can sometimes fool you into thinking something is
worse than it really is. This wear is typical and acceptable.
|
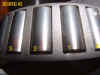 |
This bearing is totally unacceptable. Notice the dents in roller #1.
Many of those dents are deep enough to have cracked the hard surface
of the roller and all are deep enough to hold any debris that may
pass over them. Roller #2 shows a progression of wear that began
like that seen on #1. Roller #3 shows an area where the cracked hard
facing has chipped away and #4 is an example of deep spalling. As
the hard facing chips away some of those chips are pressed onto the
surfaces of the bearing race and other rollers; some of it becomes
suspended in the lubricant. Those chips pinch through the lubricant
each time a roller runs over them, produce another dent, more cracks
in the hard surfaces, and it becomes a vicious cycle of the bearing
eating itself. Never re-use a bearing that has even one small area
on one roller in the condition you see on Roller #1.
|
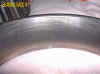 |
Here we have an unacceptable bearing
race with deep pitting and microscopic cracking of the hard face.
Notice the bearing up in the corner that had been running in this
race, it too has pitting on every roller. Another condition that is
rarely encountered on a bearing race is one that has been sitting
idle for a long period of time and has gotten moisture in it. It
will be noted as lines across the face of the race where the rollers
have contacted it. If those lines wipe away with a swipe of a rag
the bearing will be OK. If not, get a new bearing because the
rollers and their inner race suffer from the same condition, it just
can't be seen.
|
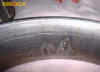 |
This is another portion of Bearing
Race #1 and shows the resultant spalling that began as pitting. What
you see here and in the other examples of pitting and spalling are not
examples of normal wear. Take another look at Bearing #1-A for an
example of normal wear. A bearing race with an appearance much like
the coloration of those rollers is an example of normal wear and is
re-usable.
|
Now. If those bad bearings are not an
example of normal wear, then just what the hell are they?
I'd like to note at this point that these
photos are of wheel bearings from my 1975 Travco Motorhome and they have a
total of only 33,000 miles on them. Never mind that they are not out of an
MGB, they are typical of the type and are bigger, and much easier to
photograph. Only one out of eight wheel bearings was bad and the cause was
dirty maintenance procedures during a brake job, or perhaps, but not likely,
a faulty bearing installed at the factory. The bad bearing and race in the
pictures was the left rear outer and thee outers have a tendency to
fall out on the floor or into a dirty drip pan when removing the rear hub.
The other three rear wheel bearings run in the same 80-90 gear lube as it
and were all in good condition. That's why I suspect dirty maintenance lead
to it's failure. I fully expect the other seven bearings to run at least
100,000 miles more.
Note:ps are actually pressed into the
surface.
Whether or not any bearings need replacing, wipe any excess grease out of the
hub, off the spindle, out of the cap that covers the spindle nut, and wipe off
the seal surface of the spindle. There's no need to wash any of these items.
In fact it's a good idea not to in order to avoid getting any grease on the
friction surfaces of the brakes.
In
the event you find a bad bearing you will have to remove the cup from the hub.
Lay the hub on a solid surface with the bad cone on the down side. You may
have to block it up with wooden blocks to allow room for the cone to exit the
hub. Look closely through the hub and you'll see the edge of the cup extending
slightly out of the edge of the hole through the hub. Many times there will be
two notches in that surface that expose nearly all of the edge of the cup and
that are there to accommodate driving the cup out.
Use
a medium hammer about the weight of a common claw hammer or smaller and a
punch to drive the cone out. Using moderate to light blows, alternate the
punch from one side of the cup to the other until it is expelled. Reverse this
procedure to install the new cup. This is a relatively slow process coming and
going, just be patient, the cup is moving with every blow and has to go
straight out and straight in or it won't go at all. When the new cup bottoms
in it's recess in the hub you'll note the sound of striking it changes from
dull to clear. That's how you know it is seated properly, listen for it.
Note: get a set off
the shelf, but will have to look up the seal.
To
pack the cleaned and/or new bearings requires nothing but the grease. You
should use actual wheel bearing grease available in 1 pound containers. The
brand name means little, the main thing is to get a grease that has a soft
buttery consistency. Black grease, containing Moly or Moly Sulfide, or
semi-synthetic grease is a plus, but not a necessity. Avoid so-called
heavy duty grease that is stiff and has a fibrous consistency.
Now
for the packing:
First get some grease on your finger and coat the inside of the hub. A moderate
coating is OK, but it isn't necessary nor recommended to pack it full. Next
wipe a thin coat on the spindle and a very thin coat on the seal surface of
the spindle. If you are right handed put a small pile of grease in your left
palm and take the large inner cone into your right, reverse this for
southpaws.
Begin
pressing the most open side of the roller cage through the edge of the grease
and against your palm. Repeat this until you have grease coming out the other
side of the roller cage and keep turning and packing the bearing until the
roller cage is full. Wipe a generous coat on the outside of the cone and drop
in into the cone in the hub. Fill the edge of the bearing with grease to about
the depth you calculate the inner side of the seal will reach. Remembering the
orientation of the seal lip, (lip toward the grease), install the new seal.
This can be done with light taps directly to the edges of the seal, but better
to use a small block of wood across the seal to avoid damage to it.
Drive the seal only to where it's outer side is level with the edge of its
recess in the hub and wipe a light coat of grease on the sealing surface. Pack
the outer bearing and lay it on a clean surface, newspaper or anything, near
the spindle and install the hub.
MGB's
have a spacer and some shims that go in the hub between the bearings. Use them
if you must, but you don't have to. These items are engineering overkill, not
really needed, and not likely to fit properly with new bearings, so we'll
leave them out and do this like it's done on a billion other cars. Tighten the
spindle nut good and snug, rotate the hub or hub/wheel assembly a couple of
turns, back the nut off until slack, and re-tighten lightly.
If a cotter pin hole lines up with the slots in the nut you're set. If not
tighten the nut ever-so slightly and check again, if the pin will go in, do
it. If still not back the nut off until it will. Give the hub/wheel a couple
of turns, press/shake it sidewise and up and down to detect any looseness. No
looseness? Bend the cotter pin to secure it. Looseness? Remove the pin,
tighten the nut to the next slot. Some spindles have two cotter pin holes, one
vertical and one horizontal. Look for this and use whichever one makes the hub
fit best.
|