Early 70’s MGB's have a combination
two-speed wiper switch with the windscreen washer function and the
overdrive on-off function on the right side of the steering column. This
switch is fairly basic in design and reasonably well built. As with most
other items on our aging beauties they eventually develop problems. But
don’t despair, they were built to be disassembled and serviced and
it’s really not hard. No special tools are required; just a clean work
space on the bench and your trusty ohmmeter. If the wipers are
intermittent or the washer pump doesn’t work or, heavens forbid, the OD
quits you might want to check the operation of the switch before you
decide to rip the car apart.
Unplug the switch’s 9-pin connector that
lurks under the left side of the dash. There will be three similar looking
plugs there; one for the turn signals, one for the ignition switch, and
one for the wiper/washer/OD. You can figure out which one is which by the
color of the wires. The yellow and white wires are for the OD. The white
wire is the hot, or supply, side, the yellow provides the voltage to the
OD solenoid when the switch stalk is pulled forward. Use a couple of
alligator clips to attach your ohmmeter’s leads to the yellow and white
wire’s pins on the connector and engage the switch. You should read very
low resistance, less than a couple off ohms at the most.
The same thing applies to the wipers and the
washer function. In the wiper’s “Off” position the red/green and the
brown/green make contact. In the wiper’s “1” position the red/green
and the green make contact and in the “2” position the green/brown and
green make contact. When the stalk is pushed in the washer pump’s light
green/black and black wires make contact. If any of these are showing a
high resistance then dive in and fix the switch. You can act French and
say “I give up” and pay over $130.00 for a new one or you can bloody
well ‘ave on wit ‘t job.
Remove the cowl from the steering column and
remove the switch. Nothing to it. If you can do that, the rest is a piece
of cake. I found that by gently rotating the back of the cowls downward
and forward they come away with a minimum of fuss
You’ll need a Phillips screwdriver, and
very small slotted screwdriver or stiff pick of some sort, some needle
nosed pliers, some alcohol or thinner to clean stuff, some 1500 grit
wet/dry, and some lithium grease. And your trusty ohmmeter.
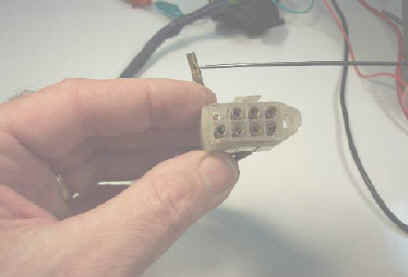
Remove the two screws from the metal
cover plate:

Here’s where you need to be careful. Hold the switch firmly so
the stalk doesn’t move and lift the cover off:
Using the small slotted screwdriver
remove the two springs from the end opposite the ball bearings. Be
careful, the springs can launch the ball bearings into outer space, or at
least some space where they’ll never be found. You can see how the ball
bearings pop in and out of the rounded notches as the switch is rotated to
hold the wiper contacts in place. The main problem with the switch
assembly is that these ball bearings and the OD’s brass spring/plunger
combo get dried out after 30+ years and bind up, breaking the plastic
parts.
Now you can ease out the stalk
assembly. Push on the two wires that come in through the back to help ease
it out. Wiggle it. Here’s what’s underneath:
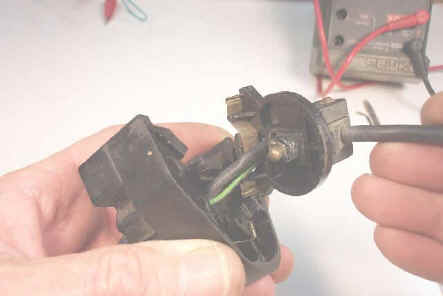
The little brass plunger has a spring
behind it and serves as a detent to hold the stalk in the OD position.
Pull the brass plunger and spring out. The thin brass band is the contact
strip that makes the wiper’s “Off, 1, 2” connection. It comes out by
lifting it away from the plastic thusly:
Set this stuff aside for cleaning. Now
let’s tackle the OD contacts. You can see how the OD switch works; the
stalk pushes it’s lower part forward to make these two contacts meet.
This transfers 12vdc to the yellow wire.
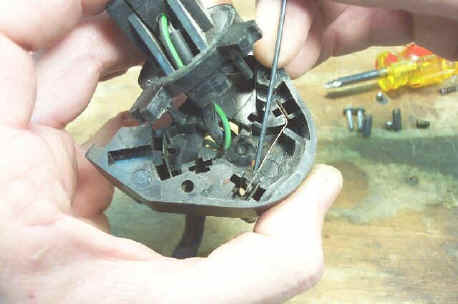
The moving contact is easy to remove
and clean; use the needle nose pliers to gently rock it up and out.
Once out you can use some 1500 to
clean the contact area. There are also two little teeth on the other end
of this strip that bite into the flat, crimped connector that holds the
wire. Clean these and using your pick, gently bend the teeth back out to
they will get a good bite when you put the contact back in.
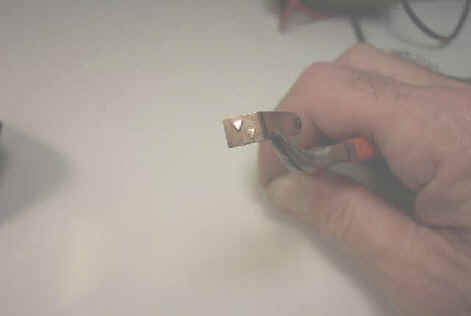
Also clean the stationary flat brass
contact that makes up the other part of the OD circuit.
At this point you can move on to the
wipers contacts. Here you can see the four flat contacts that the brass
strip makes contact with as it moves from Off-1-2. Clean these with 1500.
Clean the ends of the brass strip you removed earlier and replace it.
At this point it is a good idea to
make some resistance measurements on the contacts to see if there may be
other problems. Use the ohmmeter and measure from the flat brass contact
on the inside of the switch to the round female pin in the plug that goes
to the wiring harness. If you see more than a couple of ohms of resistance
you may need to remove those flat brass contacts and re-crimp the wires.
These flat brass contacts are held into the body of the switch by a little
tab. This tab can be pressed back into the contact with the sharp end of
the pick and the contact can be slid back out of the switch body. These
tabs are accessed through the slot directly in front of the contacts.
Gently lever the tab back toward the plate while pulling the wire. The
plate will slide right out.

The flat contact with the pick under
the tab:
You may also need to re-crimp the
female connectors in the plug. They are removed in the same manner, by
pressing the tab back into the connector:
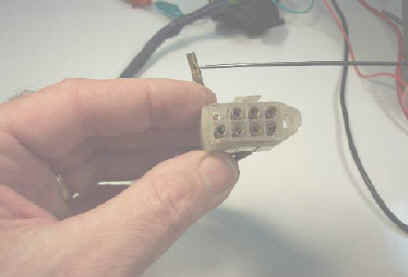
Use a standard crimping tool or needle noses
and just barely squish the part of the crimped connector where
it bites into the wire. The object is to break the corrosion on the
surface of the wire. Not much pressure is needed to accomplish this task.
You’re now ready to reassemble the
switch. Grease the brass plunger and spring that fits up into the OD
stalk’s body and fit them back in. Put a dab of grease into the socket
where the plunger fits into the body of the switch. The plunger moves in
and out of this socket as the OD part of the switch is engaged and
disengaged. Grease the two springs and ball bearings that fix the position
of the wiper switch and set them aside.
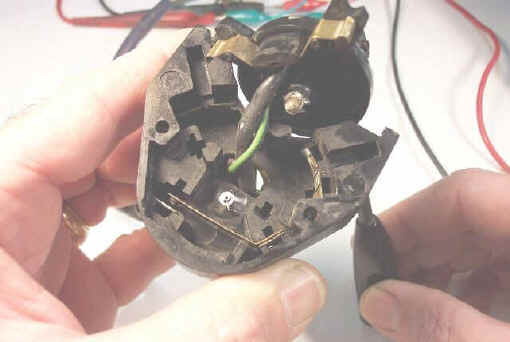
Ease the stalk section back into the
body of the switch while gently pulling the wire back through so it
doesn’t get fouled.
Now that it’s back in you can
carefully replace the springs and ball bearings. Seat them in their slots
carefully. Try no to move anything once you have them in or they’ll pop
back out.
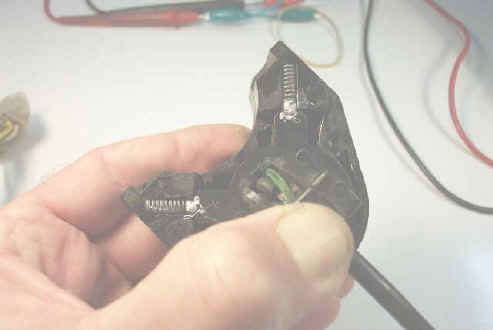
Now slide the cover back on being oh
so careful not to move the switch. Put the two screws in and you’re
done.
Once you’ve put it all back together
put the switch arm through it’s different positions to make sure
everything operates smoothly including the OD action.
The last thing to do is to clean and
check the washer pump contacts.
The metal button on the end of the
stalk unscrews to reveal it’s conical contact and the spring. The body
of this part will slide down the stalk to reveal the two fingers that the
cone makes contact with. The little copper band on the cone makes the
connection between the two fingers shown in the last pic to give 12vdc to
the washer pump.
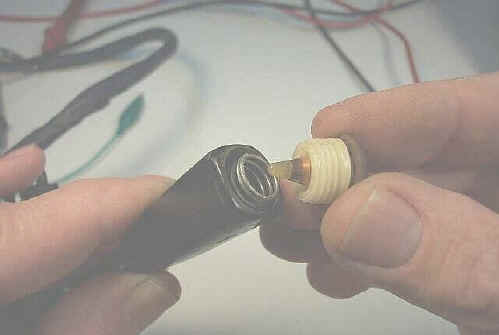
The finger contacts that the copper
band touches to make the washer pump turn on. Clean them lightly with the
1500. I use the Dremel with a fine wire wheel.
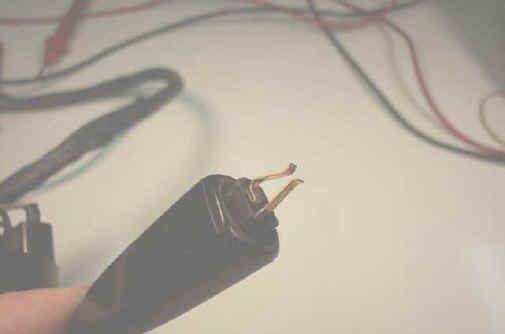
That’s about it. All that remains is
to re-install the switch back into the steering column and the plastic
cowls back over them. Be patient with the plastic cowls. You’ll find the
combination of twists and turns that make them slide right back on. Dress
the wiring harness carefully so it doesn’t keep the cowl pieces from
fitting correctly.
Take it slow and easy. It’s really a
simple switch, just lay the parts out neatly and it will be a breeze to
take apart and put back together. If you really want to make sure
everything is right test each set of contacts with your ohmmeter as you
clean them to make sure you have no resistance.
It’s a piece of cake. The biggest
job is getting the switch in and out of the car but even that’s no big
deal if you take your time. If I can do it, anyone can.
If you get stuck or need help email me
“wraylemke@compuserve.com” or call during the day (843)881-5755.
|