Wiring Modifications
|
RELOCATING FUSE
BLOCK
Wiring is an arena into which I've never ventured too far. This
modification will be my first big wiring job.
To refresh your memory: I plan to replace the original Lucas fuse block with a modern one
using plug-in fuses; and, at the same time, I'll relocate the fuse block to under the passenger
side of the dash. I also plan to replace the Lucas starter and ignition
circuit relays with modern plug-in Hella relays.
That means cutting and
splicing wires! Lots of wires!
Ian Pender sells a kit designed just for that modification. So, I
bought one. Here's what I got:

2 Hella relays w/about 1
foot of MG-color coded wire
1 4-fuse block w/about 3 feet of MG-color coded wire
Lots of different size shrink wraps
Great instructions
Before I started whacking up my "virgin" wiring harness, I
contacted my friend Wray Lemke of Charleston, South Carolina. Wray has
been playing with electrical stuff since he built his first radio when he was
eight. He's owned his own electronics service company for 22 years, and I
don't even know how to spell all the electronic things he's into. He's
also a citizen of MG-dom.
Anyway, Wray sent me the following thoughts:
|
"You can go with Lucas connectors for splicing, if you have the
correct crimping tool; or solder splice them, then heat shrink.
"To go the solder route, go to your
local industrial electronic supply house and buy a butane soldering
iron, either the Master Appliance or the Weller. They're both made
by the same manufacturer. Get the self-igniting one. It's
about $100, and is money well spent. Don't buy a Radio Shack
'u-light-em' type unit. Also, pick up a few sticks of the good,
flexible heat shrink, not that stiff crap. You'll need 1/8",
1/4", and 1/2".
"Tinning:
When we're soldering, we cut the insulation back about
1/4" on both sides, then tin the bare wire. If you run across
a wire that's slightly corroded, but still want to solder splice it, you
can gently scrape the bare strands with a knife to remove some of the
corrosion. Dip the bare wire in some Laco non-acid flux and then tin it.
It will give good results most of the time. Another trick I use
when tinning wires is to unroll about 4" of solder off the roll
then stand the roll on its side. I can then hold the wire and the
iron up to the solder and tin it.
"Shrink Wrapping: If
you have enough room, you can slide the heat shrink, that you've
pre-cut, over the wire before you tin it. But otherwise wait until
it cools, then slide it over. If it's too close to the joint,
it'll shrink from the heat transferred down the wire. Keeping it
6-8" away from the joint should be ok. Oh, your shrink should
extend about 3/4" past each side of the joint. When I do a
splice on a two wire unit, like the front turn signals, I slide my small
shrink on each wire and then slide a bigger piece on that will cover
both. I use the iron heat to shrink the small ones, then slide the
big piece over them and shrink it.
"A small vise, maybe even a Panavise is helpful at this point if
the harness is out of the car. It's much easier to make one wire
stationary and hold the other up against it when soldering. Get the two
positioned, then drag the tip of the iron across both of them at the
same time. The solder should flow. A cold, tacky joint is worse
than a butt splice. That's why we always pre-tin the wires; we
don't have to hold the wires, the iron, and the solder at the same time.
"If the harness is still in the car,
the most frustrating thing to do when soldering is trying to position
the two floppy wire ends together so they lay along side one another
when you solder them. One thought is that you could take a length
of #10 or #12 solid bare copper wire (strip some Romex) and solder or
crimp a little alligator clip lead to it. You could use this to hold one
of the wires steady by wrapping the #10 around a convenient point in the
car or use, as I have, a set of vise grips clamped to the #10 as a
base. You can then move the clip around until you can position it
to hold your work at the best angle. That leaves you holding a wire with
one hand and the iron with the other. Remember, though, to always try to
brace the hand holding the wire to steady it.
"After its cooled, feel the joint for any sharp edges that might
bite through the shrink. You can file them off or shave them with a
razor knife or clip them with a set of small cutters. I have several
small sets of Excelite cutters, they're a bit pricey but last for years.
"This joint will last forever. If it's going to be outside
where there's a possibility of getting wet, paint it with Scotchkote
when finished.
"Solder splicing is almost always superior to butt splicing.
Don't get me wrong, we do use butt splices on a regular basis but we
solder splice where we can. After you've done it a few times, it's
easy. It's only a pain when you're doing it outside, in the
winter, overhead, while hanging off a tower.
"Unlike what they say, soldering is not just like welding. It's
true you heat the work but too much of that and the insulation starts
melting. I try to make the work and the solder meet almost at the
same time, with the tip of the iron guiding the wire into the
solder. The solder should flow into the wire.
"One thing we've found is that where possible, it's better to
move any variables in wire length to the ends, rather than resolving the
lengths in the middle. In other words, if feasible, do the solder
splicing to the harness, pull the wires to the fuse block and terminate
them there. That way you can lay the wire into the path you want
without having an unsightly lump at the harness. Even if the wires
are already terminated for the fuse block, consider cutting the ends off
and re-terminating them when you're finished.
"You
could also leave a small service loop coiled up, maybe one or two turns,
behind the fuse block out of sight, should you need it later. We
always leave a service loop, and have had other service companies call
us and thank us for doing it when they had to work on the equipment.
"I'm assuming you're just extending the existing leads from
where the old fuse block went in the harness to the location of the new
fuse block and that probably the new wires are already terminated for
the new fuse block. Whack 'em off, make your splices in the engine
compartment, pull the wires back to the new fuse panel and re-terminate
them.
"Badda-Bing,
Badda-Bang...yer smokin."
|
My good buddy and a charter
member of MG-dom,
|
"It's much easier to clean and re-tape the wiring before you paint
the engine bay. Just pop that grommet from where the wires come through the
firewall and get enough slack to bring the grommet out to where you can reach
it easily. Clean and re-tape the harness with Scotch 35 blue electrical tape
from a home improvement store. Scotch 35 is the blue version of their 33 tape
and is the best electrical tape you can buy.
"Tape over all the 'solid' original tape you can. This helps keep all the 'Y's'
where they belong. Get all the wires into the groups they'll end up in.
Start at their 'roots'. Get them straight, and tape them together
every six inches or so.
"Start taping at the grommet and when you reach a
'Y' make a quick lazy spiral out to the end of the shortest branch. Make
a couple of tight turns and tape your way back to the 'Y'. When you
reach the 'Y' make several tight wraps in several directions in
order to fill the crotch and continue out the long branch. Continue out the
bundle until finished and you won't have any place for an end to come loose
because you've done the whole bundle with one piece of tape. "When that job is
finished double the long wires back toward the grommet until you have a
bundle about three feet long. loosely tape that, wrap it well in plastic
sheeting, and tape that up good. When you get ready to paint run a wire down
from a rafter or anything somewhat higher than your head and attach that
to the end of the bundle. Use the wire to suspend the bundle at about a 45
degree upward angle pointing toward the left headlight area and it will be
completely out of the way while painting"
|
Well, that seems easy enough. So, here we
go...
The first thing I have to do is cut the
wrapping off my harness around the fuse block. Wow!! Scary!!

BEFORE
AFTER
You'll notice there are some differences in the 2
photos other than removal of the harness' blue covering. The air conditioner clutch
relay hidden up behind the hood stay is gone as I don't plan on air conditioning
this car. The hood prop is also gone; remember, I'm using a custom
fiberglass MGC hood so I'll change to its hood prop later on.
Man, that harness
looked so nice and now looks so messy.
Additionally, you can see where, over the years,
I'd replaced the Lucas electronic ignition with a Crane unit without really screwing up
the wiring (the Crane unit went when I removed the 1800 engine).
|
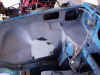 |
Earlier, I had
grafted an opening from the driver inner fender of one of my parts
cars to the passenger inner fender of my V8 car. The
interior openings in the passenger fender now mirror those in the
driver fender. It is though these openings that I'll run the
wiring harness and pull hot air from the engine compartment. |
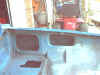 |
"But, why 1-3/4"
?" you ask.
Simple. That's the same size as the hole through which the harness
comes through the firewall. So, the same size rubber grommet will
also fit the new hole.
|
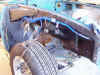 |
Here's the final
harness all taped up with nice blue tape and hanging temporarily
from small pieces of wire. You'll notice there's no fuse
block. And, you'll notice the harness is larger than
normal. That's because the fuse block has bee rerouted under
the dash and replaced with Ian's new fuse block. You'll also notice the Lucas relays have been
replaced with the modern Hella units I got from Ian. |
Next
weekend,
I'll make small hangers to permanently attach the harness to the top edge
of the inner fender so the bolts or rivets won't show from the engine
compartment side of the inner fender. I'll also relocate the rear wiring harness from under
the car to inside under the carpet ala the RV8. Why? Well, since I'm running dual exhaust, it
just seems prudent to get the wiring inside and out of its way.
|
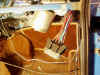 |
The new, modern fuse
block hanging under the dash in the general vicinity of the glove
box. When the dash is reinstalled and the wiper motor
secured to the firewall, the fuse block will be permanently
mounted. |
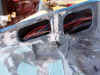 |
If you look closely
at the bottom of the large opening to the right in the photo, you
can see the original wiring harness making its way forward.
The loose wires (not yet incorporated into the harness bundle) are
the new wires needed to move the fuse block from it forward engine
compartment location to under the dash. They are why the
harness looks `so large in the earlier photo.
|
|