21 April 2003:
WOW! I've let the little car sit for almost a year while I played with
other things. Shame on me! So, here's today's story: I
rented a 34' Champ Lift to stand the trusses on my Garage-Mahal extension over
the weekend (figured I'd get them standing Saturday & drive down to
Birmingham to spend Easter Sunday with daughter0. As usual, my luck is bad
- damn thing had a short in it! After several hours, the mechanic took it
back to rental place. So, I wasted the morning and part of early
afternoon on that gadget. Should've just stood the trusses by hand!
So, I walked into my garage and
was drawn to the little GT. She's just sitting up on my Kwiklift rack.
You
know the type: you roll the car up on ramps that are then lifted about 4'
in air using a floor jack. Mine's powder coated yellow so it stands out,
and so I don't hit myself on its edges squeezing around things in my garage!
The Kwiklift makes it easy to get under a car to work on the
suspension.....suspension! That's what I'll do. I'll rebuild the
front beam! I've been planning on finishing that before I install the
rebuilt engine and transmission. So, front suspension it is!
I had another suspension beam
sitting under the car so I finished stripping it of its components, cleaned it,
and painted it black. Then, I rebuilt the lower wishbone/control arms and
painted them black. Oh, we also modified the wishbone arms by installing
zerts in their big ends so the wishbone shafts can be greased; and, new V8
bushings went in the assemblies. Then, I purchased new grade 8 bolts,
washers, and nuts to attach the wishbone assemblies to the beam.
Next, I turned to the car
itself. The first thing I needed to do was jack the car up to remove its
tires so its old beam could be dropped. Now, this lift has moveable
'saddles' spanning its 2 ramps that are used to position jacks so the car can be
jacked up off the lift. To do the jacking, however, I had to use the car's
jack points and its jack. And, that presented a problem: both jack points
were flattened out so the bar of the jack wouldn't go in them.
Several hours later, both jack
points were round again and the jack fitted as designed. How did I do
that, you ask. Well, I started with the smallest pipe I could force into
the flattened opening and worked incrementally upwards until a 3/4" pipe
would slide easily into the jacking point. All the while, I applied heat
to the jacking point so the metal would contour to the pipes while hammering on
the outside of the jacking point itself to help the metal remember its original
shape. Now, some flat black paint can be applied to the jacking points (I
was gonna do that anyway as they are Glacier White now).
So, Saturday ended with the front
tires off an the car on jack stands ready for me to drop the beam. The
newly repainted beam is beautiful as are the lower wishbone
assemblies.
Oh, I also installed the new
front bumper spring brackets (Moss #'s: 472-210 & 472-220) using new
hardware (Moss Mounting Kit #321-938) mainly to have something to hold onto as I
pull myself up from under the car.
6
May 2003 When it rains, it
pours! And I'm not necessarily talking about the weather though in this
instance, it was pouring rain. Since it had rained all day, I decided to
work on the car, removing the old suspension beam intact. I slid my engine
hoist up under the lift & inserted its tongue through the engine compartment
to grab the beam with chains. The steering rack came out easily enough as
did 3 of the 4 cross-member bolts. However, the rear driver-side
cross-member bolt - the one nearest the exhaust manifold - didn't budge. I
tried hammering it out from on top. Nothing!
So, I removed the nut from the
rear of the cross-member bolt and slid the suspension out from underneath the
car. Then, I tried moving the bolt from the bottom using an air impact
wrench and the bolt's nut. All I succeeded in doing was stripping the nut
onto the bolt! Beating with a BFH didn't budge it either way. And I
really didn't want to use heat because the engine compartment is painted, so...
I began with a 1/8"
drill bit and worked up to a 1/4" bit. However, the extractor
also didn't budge the bolt. Working up to a drill bit the size of
the bolt, I drilled through the bolt halfway down into the car's frame
member. Nothing! Apparently, the heat from the exhaust
manifold has 'welded' the bolt into its hole. I did, however,
succeed in breaking the welds on top of the frame rail that hold the
bolt's spacer in place. Now, I've gotta repaint! And I still
have to remove that bolt (or what's left of it!).
And its still raining!
19
May 2003: So, here's
the status; and, I've never faced this problem before.
I cut off the bottom of
the bolt and drilled all the way through it with a 3/8" bit.
It still wouldn't move so I went up to a 1/2" bit. Now, the
bolt is 1/2" in diameter so I stopped when I realized there was no
way to keep the bit centered. However, the bolt is really frozen
inside its "distance tube." I call it a distance
tube as it is a round tube welded through the frame rail through which
the bolt goes.
With no other options, I
cut the spot welds holding the distance tube strengthening plate
to the bottom of the frame rail and bent the plate out of the way to
gain access to the tube itself. It also was welded to the bottom
of the frame rail as well as to the top. I broke all the welds and
the distance tube (with the bolt inside it) dropped to the garage floor.
Now, I have to make a new
distance tube, weld it inside the frame rail, and insert a new
suspension beam bolt. Then the driver inner fender, the bottom of
the frame rail, and the driver side fender well have to be repainted.
LESSON:
When dropping the suspension beam, if the driver side bolt doesn't
automatically drop to the garage floor after the nut is removed, remove
the bottom nut and take the suspension beam out. Don't try to
force that suspension beam bolt from the frame rail. Accept the
fact that years of exhaust heat have welded it in place. And, when
replacing it (if it comes out), use lots of anti-seize gook!
29
September 2004: Though
I've not been posting regularly, several things have happened to Jerri's
GT since I last updated this section:
a.
The new front suspension distance tube has been welded in place and the
driver inner fender and bottom of the frame rail have been repainted. All the new front suspension bushings are
here along with new springs, tie rod ends, kingpins, anti-sway bar links, etc.
needed to build the front suspension. The suspension beam has been test
fitted - the repair was successful. This weekend the build of
the front suspension begins.
b. I've bought new front and rear wire wheel hubs along with new 14"
wire wheels. The rear hubs are under the car; the front ones go on
with the new front suspension. And, man, do those new wire wheels
look good on the new hubs with the new brake drums shining behind them.
c. I've built a complete new set of rear brakes. They're
bolted to the rear end right now.
d. There is a set of new front brake rotors sitting on my
bench alongside a pair of new front brake calipers and hoses just waiting for the front suspension to be built.
You know, that only took a
few brief paragraphs to describe. However, making the new front
suspension beam distance tube
and welding it in place occurred over several months of machine work. Then, I had to
sand and repaint places where welding the distance tube ruined the paint. Plus, I
undercoated the inside of the front and rear fenders before any suspension items
were installed. And building the complete new rear brake setups on the
bench took a few days (I mean, everything that has to do with the rear
brakes is brand new - from the backing plate out!)
And I had to hang tough
through a little harassment from Jerri when she came home from
volunteering at the local library and found me working on the rear end of
her car. "What's happened? Is it snowing somewhere
south of here? Or did you just get lost as you were wandering around
in the Garage-mahal? You're working on my car: should call
911?" You guys know the routine!
3 October
2004: This weekend we
got quite a bit done on the front suspension build. The newly
painted suspension beam with its new upper and lower mounting pads is
bolted under the car. New rebound buffers are attached to the ends
of the beam. New '74-1/2 GT springs are also temporarily located
under the beam as are the rebuilt lower wishbone assemblies (with new
bushings on the wishbone pivot end - the new kingpins and stub axles will
go on later this week).
Oh, we
also drilled the wishbone arms for grease fittings on the pivot end and
modified them internally to accept grease. We also installed new
sway bar links on the lower wishbone assemblies.
4 October
2004: Today was one of
those "dirty" days. Everything from the old suspension
that's going to be reused was filthy from age and use. Got the new
front shocks installed and then most of the day was spent cleaning nuts
and bolts; however, I did get the swivel axles disassembled and in the
cleaning tank in preparation for new king pins, bearings and bushings.
11
October 2004: Since
last I updated the site, I attempted to compress the new front springs to
assemble the new stub axle assemblies. All I did was lift the front
end off the jacks. So, I chained the car to my KwikLift so my floor
jack could compress the springs rather than lifting the car off its jacks.
First, however, before
reattempting to compress the springs, I needed to stabilize the car a bit
as all 4 corners were in the air on jack stands. So, today I had 4
new Kuhmo 185/70R14 tires mounted on the new wire wheels. The rear
wheels are now on the car, held in place on the new rear hubs by a pair of
new winged knock-offs; and, the rear of the car is sitting firmly on the
Kwiklift ramps. Tomorrow I chain the front suspension beam to the
Kwiklift and again attempt to compress the springs.
22
October 2004: Well,
chaining it to the Kwiklift didn't work either. Nor did the
suggestions of several members of MG-dom. So, I took a drawing of MG
Service Tool
This weekend we'll see it it works!
16 April
2005: Well, it didn't!
Just as the spring reached the point where I could almost fit the upper
suspension link trunnion into the shock lever, the center shaft of the
tool would slip. That, plus, I was worried about the outer arms
slipping out of the spring itself. So, off and on, I'd try
again.
We modified the tool several times
to no avail. I reread the shop manual to see exactly how Abingdon
used their spring compressor - don't try to install a spring that
way! I completely disassembled the suspension following their
directions and still got nowhere.
Finally, this morning I decided that the springs were going to compress or
they were going to shoot out of the tool and flatten my head against the
wall!
Voila!
Hallelujah!
The
springs are compressed!
And the suspension is complete! New bearings and races, new seals,
new hubs, new wire wheels, new king pin assemblies, new bushings, new
bolts...heck, everything is new! And it only took 2 thin shims in
each hub for them to turn like they were designed to do.
Don't ask me what I did differently I
can't think of anything. For some reason, everything just fell into
place. And for the first time in a long time, I can see the light at
the end of the tunnel.
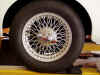
|
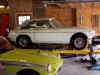
|
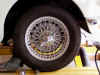
|
Tain't that new
rear wire wheel and knock-off pretty? |
On her own wheels
- new wire ones - for the first time since April 2003! |
And this new wire
wheel, woowee!
I still have to install the new brake calipers, cotter pins in the
hubs, and dust cover; but, heck, this IS progress! |
22 June
2005: The new front
brake calipers are installed along with the correct new front brake
rotors. Along with the rotors, I also installed new front brake
lines, pads and pad retaining clips and pins.
24
October 2005: Well,
today I got everything lined up to start the wiring/plumbing.
Yesterday, I temporarily put the dash together to ensure that all the
wires matched the instrument/switch locations. Up under the car, I
got everything stretched out so tomorrow I can bolt it all up with new
brackets, bushings, and bolts. Plus, the new gas tank is ready to go
under the car, after wiring/plumbing, using a new tank mounting kit.
In keeping with the car's character, I'm using a non-vented tank.
25 October 2005:
Today, I got the battery cable, brake line, and fuel line permanently
run and attached to the front half of the underbody. Remember,
this is a '71 body shell into which I've grafted late power boosted
brakes; thus, I had to reroute the brake lines along the top edge of the
engine compartment over the heater and make the connection to the
underbody line right after it turns behind the firewall, a little farther
forward than original. I also had to reroute the gas line over the
late model pedal box to a place out along the driver inner fender as the
car will have an 18V engine with dual HIF-4 carburetors; so, the fuel line
has to feed the front carb first. However, I'm leaving the fuel
filter mounted on the firewall between the heater and the pedal box.
I don't know why I did it; however, back when I did the body, I used an
aftermarket floor that doesn't have locators for seats, plumbing, etc.
built in. I probably had a new one on hand at the time and it was
just easier to take it to the body shop after we sandblasted the car than
to wait for one to arrive from Moss. Now, however, I'm 'paying the
piper' as I've got to do some drilling and welding to fit the plumbing
underbody grommets and retaining straps to the rear half of the
underbody. Oh, well, tomorrow's another day! Hopefully, by
tomorrow's post, all will be mounted and I can turn to the gas tank.
26 October 2005:
Wiring harness is finished all way back to (& in) the hatch
floor! Brake line is hooked up to the rear brakes! Fuel line
is run to where the new fuel pump will be located! Battery cable is
back to the passenger-side battery box! And the battery ground strap
is converted from dual battery setup to single battery in the
passenger-side box!
30 October 2005:
Finished! Wiring! Plumbing! New gas tank!
5
November 2005: Hard
pipes run from gas tank to fuel pump; gas tank filler tube, new gas cap,
and filler neck ferrulle hooked to new gas tank; new sending unit
installed. New SU fuel pump installed with new banjos and flex line
to under floor piping. WHEW!
|